
Table 4: Results Comparison 3D PILE RAFT FOUNDATIONKeywords: EPS, Plaxis 2D, Geofoam, Embankment 1. The RS2 results compare well with the PLAXIS 2D results from Ryltenius (2011) as shown in Table 4 below. Figure 5: Axial Force Distribution of First Two Piles. Only the first two piles are shown due to symmetry. The distribution of the axial forces for the two piles are shown in Figure 5 below.
Embedded piles comprise of beam elements and have special interfaces. Both methods have some advantages compared to each other, but both also have clear drawbacks: Plate elements have pile properties, convertedIn PLAXIS 3D, the user can select between volume piles and embedded piles to model a pile foundation. It is an extremely low density, a high strength two weight ratio and gives very small 10 Plaxis Bulletin l Autumn issue 2013 l In the past, plates and node-to-node anchors have been used to model piles in PLAXIS 2D.
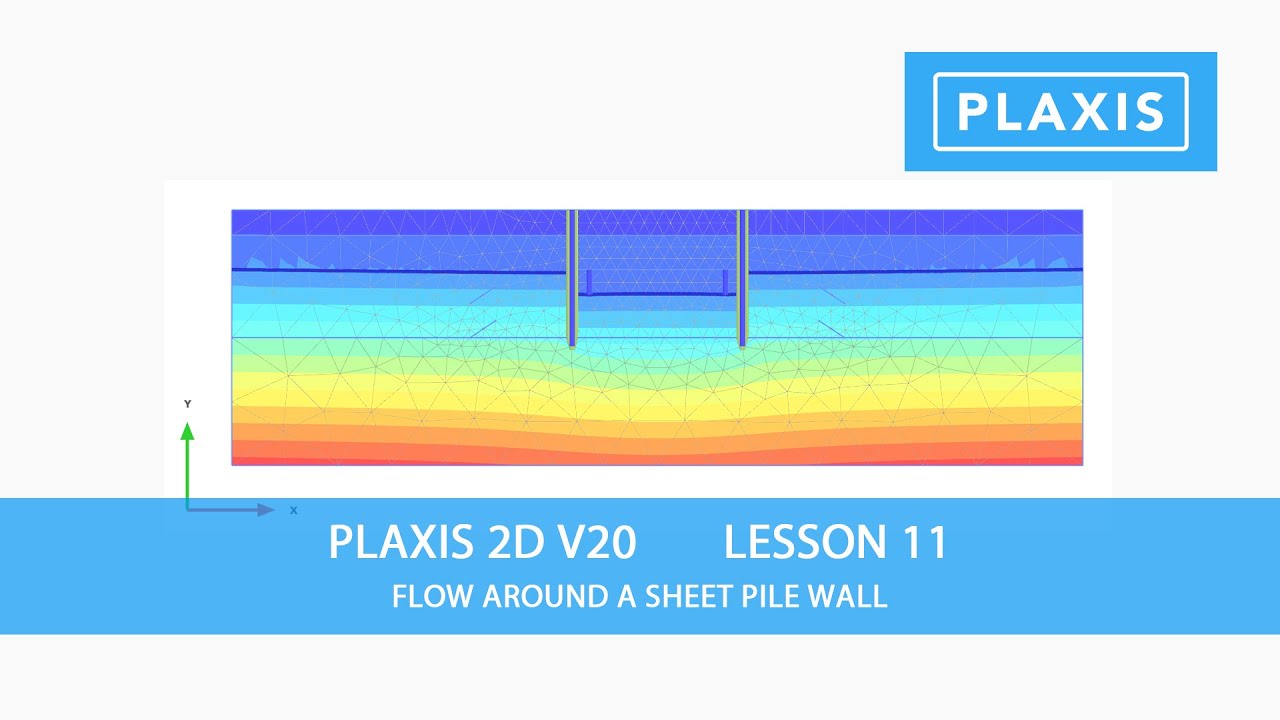
It has pile properties similar to the plate element and a continuous mesh similar to a node-to-nodeAnchor. Some sort of pile foot modelling is needed in order to sustain axial forces in the pile, since a single node at the foot is gener-ally insufficient and leads to mesh dependent results.The embedded pile row combines the advantages of the plate and node-to-node anchor. Moreover, a node-to-node anchor has no properties in lateral direction, which lim-its the use of this method to fully axial loaded piles only.
This article discusses the principle and validation of the feature, which has been performed in a MSc thesis study (TU Delft). It is supposed to result in a more realistic pile-soil interaction behaviour compared to other methods. The embedded pile row has been developed to model a row of piles in the out-of-plane direction, which is available in PLAXIS 2D 2012. Pile-soil interaction is difficult to model and traditional methods in which pile rows are modelled either as plates or as node-to-node anchors have clear drawbacks. A special out-of-plane interface is developed to connect the beam with the soil nodes and represents the pile-soil interaction.The modelling of piles in a 2D finite element model brings limitations because pile-soil interaction is a strongly 3D phenomenon. The pile, represented by a Mindlin beam element, is not in the 2D mesh, but superimposed on the mesh.
There is no limitation of the spring forces in lateral direction. The springs in axial direction are limited by a plastic slider, representing the shaft capacity of the pile. 1: Principle of the embedded pile row (Sluis, 2012)Along the pile there is a line-to-line interface represented by springs with numerical stiffnesses in axial and lateral direction (RS and RN). The original and duplicate nodes are connected with interface elements.Fig. The element edges and nodes along the geometry line are duplicated. If a mesh is generated, the elements are generated around the geometry line.
Default values have been derived by Plaxis as part of the validation (Sluis, 2012) and are related to the out-of-plane spacing and pile diameter:The interface stiffness factors can be overruled by the user, because the formulas are derived for only a limited number of cases. The interface stiffnesses RS, RN and KF are related to the shear modulus of the soil Gsoil and the out-of-plane centre-to-centre distance Lspacing and radius of the pile r:ISFxx is the interface stiffness factor, a dimensionless factor to manipulate the deformation behaviour. This is done by using the out-of-plane centre-to-centre distance of the pile row Lspacing, which is also an input parameter.The deformation behaviour between the pile andThe soil is an interaction between pile stiffness, soil stiffness and interface stiffness, as shown in Figure 1. These pile properties are entered per pile, which are converted to properties per unit width in out-of-plane direction during the calculation. The pile capacity is defined in the material set, together with the stiffness, weight and dimensions of the pile. The interface is visualised in Figure 1 (sliders are not shown in this figure).The pile capacity is an input parameter, similar to the embedded pile in PLAXIS 3D, for which a shaft capacity TS max and base capacity Fbot max should be defined.
3: 2D soil displacement at surface level for varying interface stiffness, compared to (average) 3D soil displacement (Sluis, 2012)12 Plaxis Bulletin l Autumn issue 2013 l Validation and Application of the Embedded Pile Row-Feature in PLAXIS 2DBecause installation effects are not taken into account in PLAXIS, the embedded pile row is most suitable for bored piles. 2: Modelling of a pile row with a single embedded pile in PLAXIS with various pile spacing (Sluis, 2012)Fig. The behaviour of the embedded pile row, soil displacement and pile displacement, was evaluated for four loading directions: Axial compression loading Axial tension loading Lateral loading by external forceFig.
In 2D, the force should be divided by the pile spacing. For larger pile spacing, the results deviate from 3D calculations, which is probably caused by the absence of a plastic slider in lateral direction.For example, in 3D a large horizontal force on top of the pile results in soil failure near the pile top, which results in the pile being pulled through the soil, giving large deformations. When using ISFRN = ISFRS, a satisfying fit is obtained for relatively small pile spacing (Lspacing/Deq < 4).
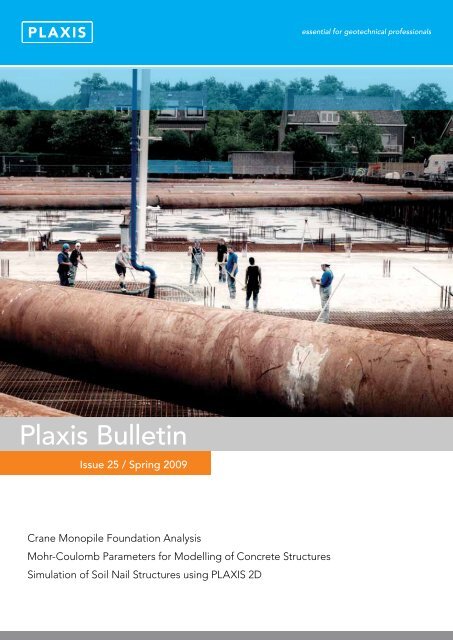

